Case Study: Wylie Distribution
THE CLIENT
Wylie Distribution is a leading provider of industrial and commercial supplies, including including electrical supplies, plumbing supplies, HVAC supplies, construction supplies, safety supplies, tools and equipment. Wylie Distribution serves a wide range of customers, including: contractors, manufacturers, maintenance and repair shops, government agencies and educational institutions.
THE CHALLENGE
Wylie Distribution was struggling to keep up with the increasing demand from it's clients, due in large to an inefficient and error prone process for ordering and managing inventory and fulfilling orders. Back in 2006, Wylie implemented a storage and inventory management system that included cardboard boxes, wooden crates, paper records and spreadsheets. The cardboard boxes were easily damaged and unreliable, frequently needing to be
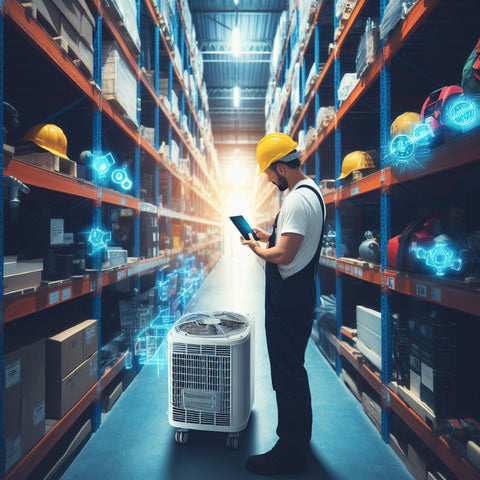
replaced. The wooden crates were heavy, bulky and always in the way. Updating records with paper documents instead of scanning and automation made it nearly impossible to track inventory levels in real time, often leading to stockouts and delays in order fulfillment.
THE PROPOSED SOLUTION
The solution we proposed had the following intended benefits for Wylie Distribution: easy to access, organize, and locate inventory combined with real-time inventory tracking and reduced inventory outages. The ultimate benefit would be a returning customer that continues to increase their annual spend with Wylie.
To make those benefits a reality, we implemented a new inventory system that used open front plastic storage bins, steel shelving and barcode scanning technology. The new system would allow Wylie Distribution to fill their warehouse with efficient order picking systems strategically positioned to maximize efficiency and reduce human errors. The shelf bin organizers made it easy to color code inventory and maintain an eye on the highest volume movers.
THE RESULTS
Wylie Distribution implemented the new inventory system proposed by Industrial 4 Less. The new bin shelving system has resulted in a number of positive outcomes, including:
Increased order fulfillment efficiency by 15%
Reduced inventory loss by 7%
Increased average order value and customer retention rate.
ADDITIONAL INFO
In addition to the metrics listed above, Wylie Distribution has also reported the following benefits from the new inventory system: Improved employee productivity, reduced worker fatigue, fewer workplace safety incidents and improved communication and collaboration between departments
CONCLUSION
The implementation of Industrial 4 Less's proposed solution has been a success for Wylie Distribution. The new inventory system has helped the company to improve its order fulfillment efficiency, reduce inventory loss, increase average order value, and improve customer retention.
